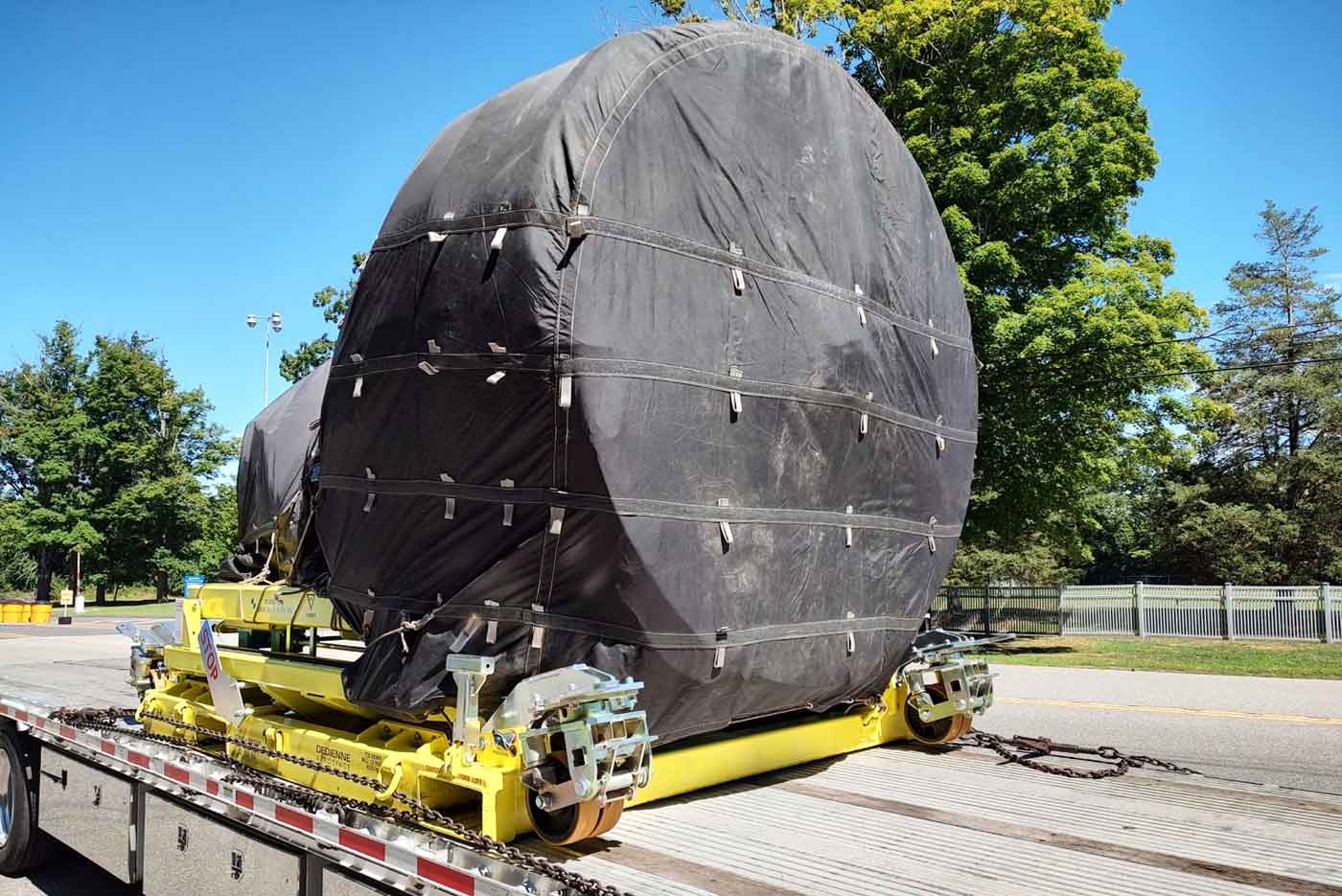
Manage your assets reliability risk thanks to predictive maintenance
Modern businesses are in a time of unprecedented change and competition. Gaining competitive edges through smart solutions can make a huge difference for aviation stakeholders which are always running after cost efficiency and asset management.
A digital solution which predict when tooling maintenance is needed can help companies to streamline their tooling maintenance operations and incidents that could have been avoided.
Predictive maintenance technologies let you hear what your tooling are trying to tell you.
Tooling Lifecycle Optimization
Tooling need regular maintenance to be up-to-date with periodic certification, repair or upgrades. The aircraft and the engines versions evolve regularly, and the tooling may need some mandatory upgrades during their lifecycles.
The difference between scheduled and unscheduled maintenance tasks is simple. Scheduled maintenance is planned for a specific time and scenario while unscheduled maintenance, on the other hand, is a more reactive approach that is utilized when a tooling is unserviceable.
Taking care of your tooling lifecycle with generic schedules and not after something fails will keep your costs down and production up.
Regular maintenance for optimal performance
With the tooling park upload on ToolLive platform, the customer can see all tooling relevant information: history, certificates of conformity, latest documentation… Alerts will be sent to accommodate and anticipate repair times (for example annual periodic certification) and material requirements (for an engine stand, shocks absorbers must be replaced every 5 years). This predictive maintenance process allows a better tooling lifecycle thanks to historical data and tooling technical knowledge.
Taking care of your tooling lifecycle with generic schedules and not after something fails will keep your costs down and production up.
Related posts
How asset tracking will create more added value for your company?
The world has changed since the Wright brothers performed maintenance on their f
How to escape the nightmare of spreadsheets?
If you ask someone how to make the inventory of their tooling the right way, you